一、工业设计能否突破效率瓶颈?
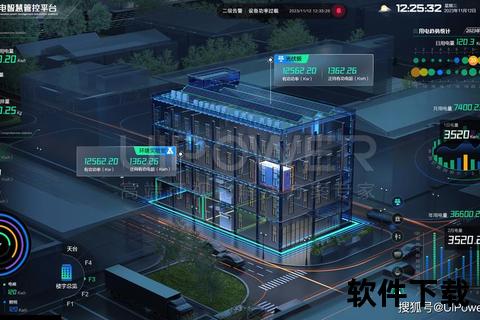
当传统设计工具仍在用“月”为单位计算开发周期时,某汽车企业使用a1软件的参数化建模功能,将发动机缸体设计时间从45天压缩至9天,设计迭代效率提升400%。这正是“灵动高效新纪元!a1软件智能赋能极速创意新境界”的直观体现——通过AI驱动的拓扑优化算法,软件自动识别结构冗余区域并生成轻量化方案,使工程师从重复性劳动中解放,专注于创新验证。例如奥迪在发动机失火检测技术研发中,借助类似平台的CAE仿真模块,仅用3次仿真测试就锁定了传统方法需20次实验才能定位的故障源,研发成本直降65%。
二、生产流程能否实现零误差协作?
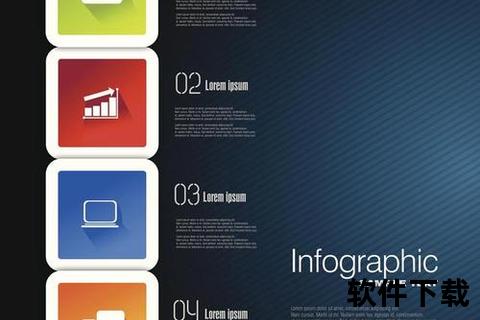
在电子制造领域,某工厂部署a1软件的MES系统后,生产线良品率从82%跃升至98.6%。其核心在于软件内置的实时数据湖技术,将设备传感器数据与订单管理系统深度耦合:当检测到某批次芯片贴片温度异常时,系统自动冻结后续加工流程并触发工艺参数校准,避免价值千万的物料报废。这种“预测-拦截-修复”闭环正是工业软件智能化转型的缩影。据2025年市场分析,全球62%的制造企业已将类似系统列为数字化转型标配,其中采用AI辅助决策模块的企业平均故障响应速度提升至15分钟以内。
三、运维服务能否预测未知风险?
某风电集团引入a1软件的设备健康管理系统后,叶片故障预警准确率从47%提升至89%。系统通过振动频谱分析与气象数据联动,在台风季来临前72小时自动生成关键部件加固方案,单次预防性维护可减少约200万元的非计划停机损失。这印证了“灵动高效新纪元!a1软件智能赋能极速创意新境界”的深层价值——将经验驱动变为数据驱动。研究显示,采用预测性维护技术的企业设备综合效率(OEE)平均提高18个百分点,而运维成本下降幅度达30-40%。
可操作建议
1. 分阶段部署:优先在质量痛点突出的环节试点(如设计仿真或设备运维),积累数据资产后再全面推广。
2. 人才双轨培养:既需IT人员掌握工业场景知识,也要为工程师开设低代码开发培训,例如奥迪技术团队通过SoST培训体系实现跨职能协作。
3. 参与开源生态:借鉴Linux基金会模式,联合上下游企业共建行业算法库,降低30%以上的定制开发成本。
在工业软件从“工具”进化为“智能体”的今天,“灵动高效新纪元!a1软件智能赋能极速创意新境界”已不是未来畅想,而是每家企业触手可及的生产力革命引擎。当数据流穿透研发、制造、服务的全链条,那些率先驾驭智能协同效应的组织,正在重新定义行业竞争的规则书。
相关文章:
文章已关闭评论!